Opening the Power of Welding WPS: Methods for Performance and Safety And Security in Manufacture
In the world of manufacture, Welding Treatment Requirements (WPS) stand as the foundation of welding procedures, dictating the required steps for accomplishing both efficiency and safety in the fabrication process. Understanding the intricacies of WPS is paramount to using its complete possibility, yet lots of companies have a hard time to unlock real power that lies within these records (welding WPS). By diving right into the techniques that enhance welding WPS, a world of boosted performance and increased security awaits those happy to discover the nuances of this essential aspect of fabrication

Significance of Welding WPS
The importance of Welding Treatment Requirements (WPS) in the construction industry can not be overemphasized. WPS work as an important roadmap that outlines the essential actions to guarantee welds are performed continually and properly. By defining crucial specifications such as welding processes, products, joint styles, preheat temperatures, interpass temperature levels, filler metals, and post-weld warmth treatment requirements, WPS supply a standardized strategy to welding that improves efficiency, high quality, and safety in manufacture processes.
Adherence to WPS aids in accomplishing harmony in weld high quality, reducing the probability of defects or architectural failures. This standardization likewise facilitates conformity with industry guidelines and codes, ensuring that produced frameworks satisfy the called for safety criteria. Moreover, WPS paperwork enables welders to duplicate effective welding procedures, causing regular results throughout various projects.
Fundamentally, the meticulous advancement and rigorous adherence to Welding Treatment Specs are vital for upholding the stability of bonded frameworks, protecting against possible hazards, and supporting the online reputation of manufacture business for providing top notch product or services.
Crucial Element of Welding WPS
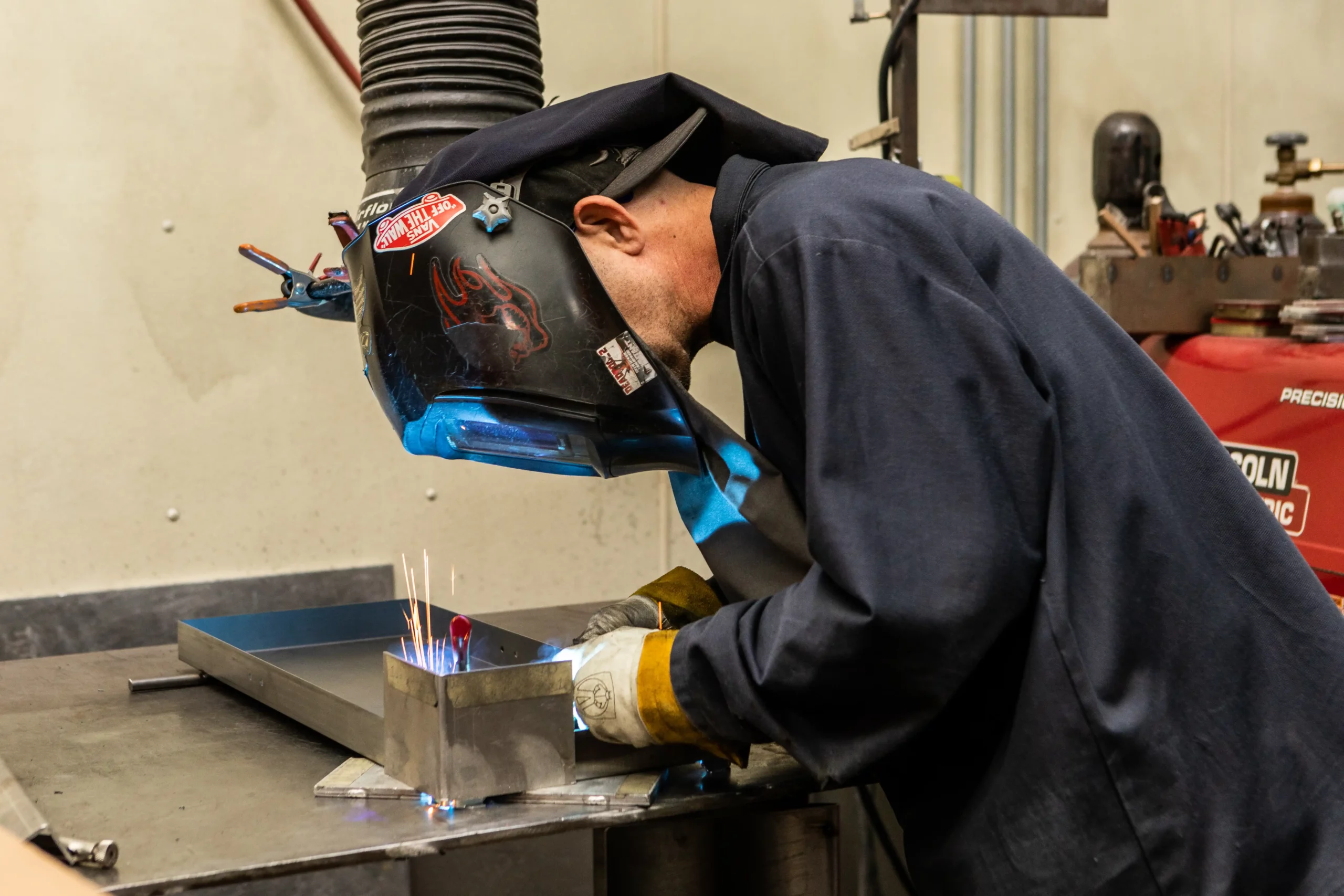
Enhancing Effectiveness With WPS
When maximizing welding procedures, leveraging the crucial aspects described in Welding Procedure Requirements (WPS) comes to be necessary for enhancing processes and making the most of efficiency. One way to boost effectiveness with WPS is by thoroughly selecting the ideal welding specifications.
On a regular basis evaluating and upgrading the WPS to include any lessons found out or technical developments can additionally add to efficiency enhancements in welding procedures. By embracing the guidelines established forth in the WPS and constantly seeking ways to optimize procedures, makers can achieve higher effectiveness degrees and premium end results.
Ensuring Security in Manufacture
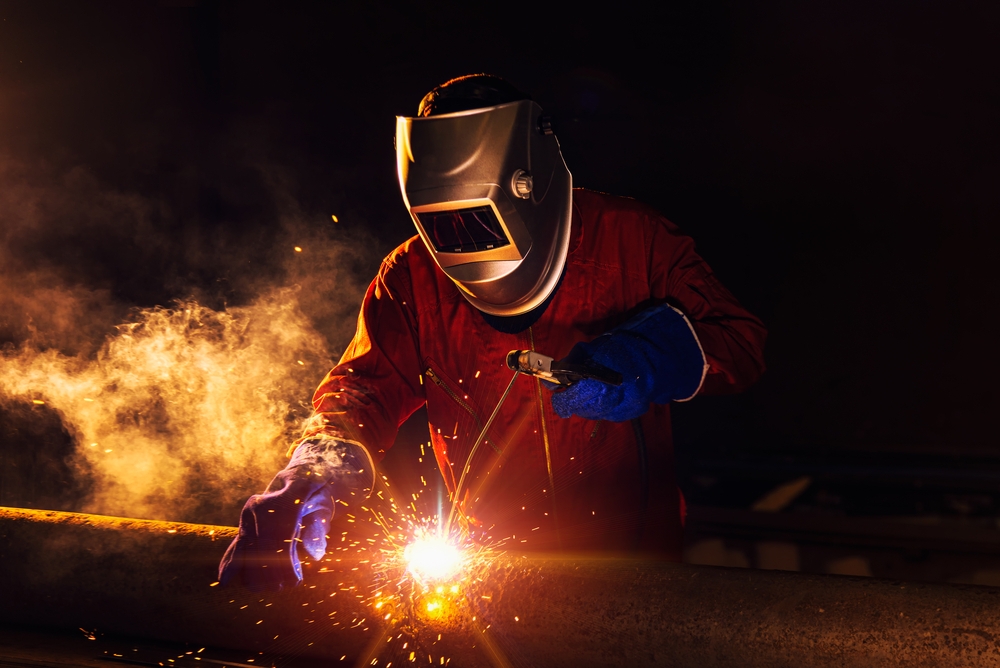
Ensuring safety and security in construction entails a diverse method that incorporates different aspects of the welding procedure. Welders should be outfitted with proper gear such as safety helmets, gloves, and safety clothing to minimize risks linked with welding activities.
In addition, adherence to appropriate air flow and fume extraction systems is critical in preserving a healthy and balanced workplace. Welding fumes include unsafe compounds that, if breathed in, can position significant health threats. Implementing efficient air flow steps aids to minimize direct exposure to these unsafe fumes, promoting hop over to these guys respiratory system health among employees.
Regular devices upkeep and inspections are likewise crucial for ensuring security in manufacture. Faulty machinery can cause injuries and accidents, highlighting the relevance of prompt fixings and routine checks. By prioritizing precaution and cultivating a culture of awareness, construction centers can develop a efficient and safe job setting for their employees.
Implementing WPS Best Practices
To enhance operational effectiveness and make sure high quality end results in manufacture procedures, including Welding Treatment Requirements (WPS) ideal techniques is paramount - welding WPS. Implementing WPS best practices involves meticulous planning, adherence to industry standards, and continuous surveillance to assure optimum outcomes. To sites start with, choosing the proper welding process, filler material, and preheat temperature specified in the WPS is crucial for achieving the wanted weld top quality. Second of all, making sure that qualified welders with the required certifications execute the welding treatments according to the WPS standards is necessary for consistency and reliability. Routinely upgrading and assessing WPS papers to show any type of procedure enhancements or adjustments in products is additionally a vital ideal method to maintain accuracy and importance. Furthermore, providing comprehensive training to welding employees on WPS demands and best techniques promotes a culture of safety and security and high quality within the fabrication setting. By carefully implementing WPS ideal methods, fabricators can enhance their operations, decrease errors, and deliver remarkable products to fulfill client assumptions.
Conclusion
To conclude, welding WPS plays a crucial function in making certain efficiency and security in manufacture processes. By concentrating on crucial elements, enhancing effectiveness, and applying best practices, business can maximize their welding procedures. It is necessary to prioritize precaution to stop mishaps and make sure a smooth manufacturing procedure. By following these techniques, services can open the complete possibility of welding WPS in their fabrication operations.
In the realm of construction, Welding Procedure Specs (WPS) stand as the backbone of welding operations, dictating the necessary steps for achieving both efficiency and safety and security in the manufacture procedure. By specifying necessary criteria such as a knockout post welding procedures, materials, joint styles, preheat temperatures, interpass temperatures, filler steels, and post-weld warmth therapy demands, WPS supply a standardized method to welding that enhances effectiveness, high quality, and safety in fabrication procedures.

When optimizing welding operations, leveraging the crucial elements described in Welding Treatment Specifications (WPS) ends up being crucial for optimizing and simplifying processes efficiency. (welding WPS)
Comments on “Welding WPS: Typical Errors to Avoid and How to Correct Them”